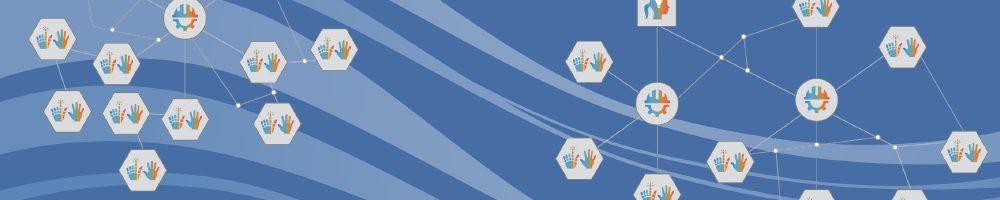
Manufacturers in the UK are reporting growing talent shortages as they struggle to find the right blend of technical and soft skills to fill new positions. In fact, as many as 81% of manufacturers are having trouble finding staff with the right skills mix and experience. With the move to Generation Three of Manufacturing ensuring that new roles are appearing as fast as others become obsolete, and strong head winds in the UK market continuing to affect this space, the manufacturing industry needs to rethink their talent strategies in order to continue to find the right people to drive business success for the future.
So what can manufacturers do to fill the skills gap for their organisations?Managing Employer BrandManufacturing companies work hard to build and maintain their relationships with existing and potential customers, often putting significant budgets behind it. However, what is often overlooked is strengthening their employer brand. With continued low levels of unemployment, workers are in the driving seat when looking for new positions, and manufacturers need to work harder to differentiate their employee value proposition – both against their manufacturing competitors and in the wider market.
Once manufacturers have attracted candidates, they often fall down at the next hurdle – the candidate experience. Our research shows that a negative hiring experience makes an individual less likely to buy from the brand in future. 61% would also tell others about a negative hiring experience.
For a worker, it is easier than ever to find out what it’s like to work for an organisation. With the success of websites like Glassdoor and Indeed Company Reviews, individuals can develop an intimate understanding of the culture of your organisation, without ever stepping foot in the building. This can often be a key influencing factor in deciding whether to apply for a position with your business, or to look elsewhere.Diversifying Workforce ModelsOften considered a more traditional industry, manufacturing typically prefers PAYE workers. But with the industry changing so rapidly and candidates often preferring something other than a full-time job, the industry needs to diversify the workforce models it’s using. Not everyone wants to work as a full-time, permanent employee, and it doesn’t always work best for organisations either.
At present, contractors are typically brought in to manufacturing environments to fix specific process issues, making IT upgrades, and manage digital transformations. However, many organisations aren’t taking full advantage of the quick injection of fresh skills and experience that a contractor can bring to the wider business. Managed correctly, contractors can be used to ‘build’ your existing talent – upskilling your permanent workforce and, potentially, improving their job satisfaction as a result.
The niche skills and increased flexibility that comes with a contractor can provide significant benefits to an organisation. It can also help manufacturers access more diverse talent pools, who aren’t able to work the traditional 9-5. However, there are other factors that organisations must consider. In April 2020, the Government will reform the off-payroll working rules (IR35) in the private sector, placing some important responsibilities on medium and large employers. Whilst guidance for these changes is still in the pipeline, it’s important that organisations start to prepare for IR35 now and factor this into their future workforce planning.
Of course, contractors aren’t the only alternative workforce model that manufacturers should be considering. Temporary, freelance, gig, on-demand and platform working are workforce models which are rising in popularity. However, given that flexible work times aren’t always suitable when you’re running manufacturing operations, employers should also consider other solutions, such as Employed Consultants. Employed Consultants are a hybrid of permanent workers and contractors – offering organisations a skilled worker who’s permanently employed by us, and ready to work in interim or project positions. And, because they’re permanently employed by us, there are no co-employment or IR35 risks.
Aligning your HR and procurement functions will help to manage this rebalancing of the workforce, helping you to prioritise talent over internal definitions, labels and reporting lines.Maturing Your MSPWith the scale of changes happening in manufacturing, employers need to focus on their core business to ensure that they continue to be successful in the future. However, talent is a key component of this, and it requires significant planning to get right.
Many MSP’s help to manage this process to some extent, but the relationship is often reactive and transactional. By working with your MSP provider to mature your MSP model and develop a strategic partnership, they can help you to get the most from your talent. Done right, the recruitment strategy should align to your annual business plan, with your provider taking a proactive approach to helping you to find and develop the best talent, and advising you on the workforce models you will need to adopt to help achieve the right business results.
This level of trust and integration takes time to achieve. But starting out with this intention will help organisations to deliver against their business goals, with a partner who knows their talent needs and can support them in achieving them.
Manufacturing organisations that embrace non-traditional employment models today will be better positioned to attract and retain in-demand talent in the future. If you would like to find out more about how we could support your organisation in adopting alternative workforce models, get in touch today.
Alternatively, to learn more about the ways in which the manufacturing workforce will need to evolve in the years ahead, download our whitepaper The Future Factory: Mapping The Skills That Will Power Manufacturing.JTNDJTIxLS1IdWJTcG90JTIwQ2FsbC10by1BY3Rpb24lMjBDb2RlJTIwLS0lM0UlM0NzcGFuJTIwY2xhc3MlM0QlMjJocy1jdGEtd3JhcHBlciUyMiUyMGlkJTNEJTIyaHMtY3RhLXdyYXBwZXItODM4OGNlMzItZTMxMS00ZjRlLWFlZTEtMWFiZmEwODY0ZTJkJTIyJTNFJTNDc3BhbiUyMGNsYXNzJTNEJTIyaHMtY3RhLW5vZGUlMjBocy1jdGEtODM4OGNlMzItZTMxMS00ZjRlLWFlZTEtMWFiZmEwODY0ZTJkJTIyJTIwaWQlM0QlMjJocy1jdGEtODM4OGNlMzItZTMxMS00ZjRlLWFlZTEtMWFiZmEwODY0ZTJkJTIyJTNFJTNDJTIxLS0lNUJpZiUyMGx0ZSUyMElFJTIwOCU1RCUzRSUzQ2RpdiUyMGlkJTNEJTIyaHMtY3RhLWllLWVsZW1lbnQlMjIlM0UlM0MlMkZkaXYlM0UlM0MlMjElNUJlbmRpZiU1RC0tJTNFJTNDYSUyMGhyZWYlM0QlMjJodHRwcyUzQSUyRiUyRmN0YS1yZWRpcmVjdC5odWJzcG90LmNvbSUyRmN0YSUyRnJlZGlyZWN0JTJGNDY3NDY0MCUyRjgzODhjZTMyLWUzMTEtNGY0ZS1hZWUxLTFhYmZhMDg2NGUyZCUyMiUyMCUyMHRhcmdldCUzRCUyMl9ibGFuayUyMiUyMCUzRSUzQ2ltZyUyMGNsYXNzJTNEJTIyaHMtY3RhLWltZyUyMiUyMGlkJTNEJTIyaHMtY3RhLWltZy04Mzg4Y2UzMi1lMzExLTRmNGUtYWVlMS0xYWJmYTA4NjRlMmQlMjIlMjBzdHlsZSUzRCUyMmJvcmRlci13aWR0aCUzQTBweCUzQiUyMiUyMHNyYyUzRCUyMmh0dHBzJTNBJTJGJTJGbm8tY2FjaGUuaHVic3BvdC5jb20lMkZjdGElMkZkZWZhdWx0JTJGNDY3NDY0MCUyRjgzODhjZTMyLWUzMTEtNGY0ZS1hZWUxLTFhYmZhMDg2NGUyZC5wbmclMjIlMjAlMjBhbHQlM0QlMjJEb3dubG9hZCUyMFRoZSUyMFJlcG9ydCUyMiUyRiUzRSUzQyUyRmElM0UlM0MlMkZzcGFuJTNFJTNDc2NyaXB0JTIwY2hhcnNldCUzRCUyMnV0Zi04JTIyJTIwc3JjJTNEJTIyaHR0cHMlM0ElMkYlMkZqcy5oc2N0YS5uZXQlMkZjdGElMkZjdXJyZW50LmpzJTIyJTNFJTNDJTJGc2NyaXB0JTNFJTNDc2NyaXB0JTIwdHlwZSUzRCUyMnRleHQlMkZqYXZhc2NyaXB0JTIyJTNFJTIwaGJzcHQuY3RhLmxvYWQlMjg0Njc0NjQwJTJDJTIwJTI3ODM4OGNlMzItZTMxMS00ZjRlLWFlZTEtMWFiZmEwODY0ZTJkJTI3JTJDJTIwJTdCJTdEJTI5JTNCJTIwJTNDJTJGc2NyaXB0JTNFJTNDJTJGc3BhbiUzRSUzQyUyMS0tJTIwZW5kJTIwSHViU3BvdCUyMENhbGwtdG8tQWN0aW9uJTIwQ29kZSUyMC0tJTNF